
Photo courtesy of Robin Gentry/iStock/Getty Images Plus and eyecrave productions /iStock/Getty Images Plus
5 steps to consider when designing a wastewater system
How to choose and size a wastewater pump, plus other crucial considerations for efficient operation.

Wastewater systems play a critical role in water and sewage management, but many things can get in the way of their effective operations. For instance, organic solids, rags, wipes and other waste matter are all too frequent challenges when it comes to wastewater pumps, while incorrectly sizing a pump can cause issues such as sewage water backing up or water not pumping quickly enough.
As a result, designing a wastewater system requires careful consideration of a range of factors to ensure efficient and compliant operation.
Where to start
Although online sizing tools can be a beneficial resource for selecting and sizing a pump for a specific application, this is only half the battle when designing a wastewater system. For instance, it’s important to also understand the methods involved in choosing the right pump, and how the pump fits in to the overall health and efficiency of a wastewater removal system.
Below are five steps that should be considered when selecting and sizing wastewater pumps.
1. State and local codes
Navigating the complex landscape of wastewater requires factoring in state and local codes, which play a crucial role in specifying the type of wastewater system and equipment required for a specific location. For instance, in Wisconsin, specific guidelines outlined in the Wisconsin Department of Safety and Professional Services chapter SPS 383.43 require an estimate of wastewater flow of combined graywater, clear water and blackwater to be calculated based on occupancy, usage and function of the property.
These codes may be furthermore influenced by factors such as soil composition and environmental regulations and may also have a requirement for solid handling size. For instance, certain soil types with better draining capabilities allow more efficient wastewater filtration, while other soil types, like those high in clay content, may have poor drainage properties which can lead to an accumulation of wastewater or an increased risk of contamination. Consulting with the Environmental Health Department in the jurisdiction of the wastewater system is essential to ensure compliance with relevant codes and regulations. The Sump and Sewage Pump Manufacturers Association (SSPMA) also has a helpful guide online for sizing new or replacement sewage pumps. Always prioritize compliance with state and local codes over manufacturer recommendations.
2. Determining solid handling size
Once you have a clear grasp of state and local compliance, another main factor in selecting the type of pump needed for handling and for your specific application is understanding the size of solids present in the wastewater.
- Sump pumps are designed to handle clear water with minimal solids, typically up to 1/2 inch;
- Effluent pumps are designed for partially or completely treated wastewater with solids generally up to 1 inch in size. This does not include large solids and is sometimes referred to as “grey water;” and
- Sewage pumps are intended to handle household waste with larger solids, typically ranging from 1 to 2 inches.
For example, if choosing a pump for a sewage application, solid handling size required would be 1 1/4 to 2 inches. Once the size is determined, then explore the type of sewage pump needed. There are three main categories for sewage pumps, including non-clog, vortex and grinders.
Non-clog pumps have impellers with tight clearances, allowing most of the material to pass through the veins without clogging. However, despite the name, they can still be susceptible to increased chances of clogging compared to other sewage pump types.
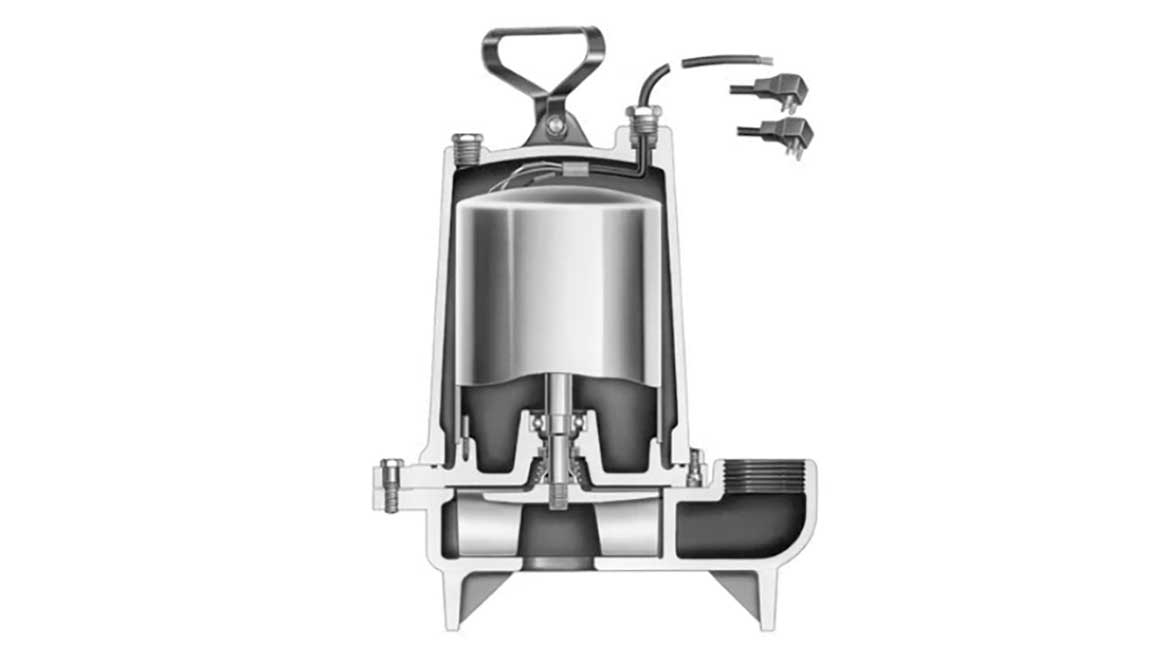
A non-clog pump. Courtesy of Goulds Water Technology
Vortex pumps have a recessed impeller design that creates a vortex, pushing the waste out without it directly passing through the impeller. This design is less prone to clogging, especially with disposable waste items like “flushable” wipes. However, they may provide less head (TDH) due to the larger gap between the impeller and the volute.
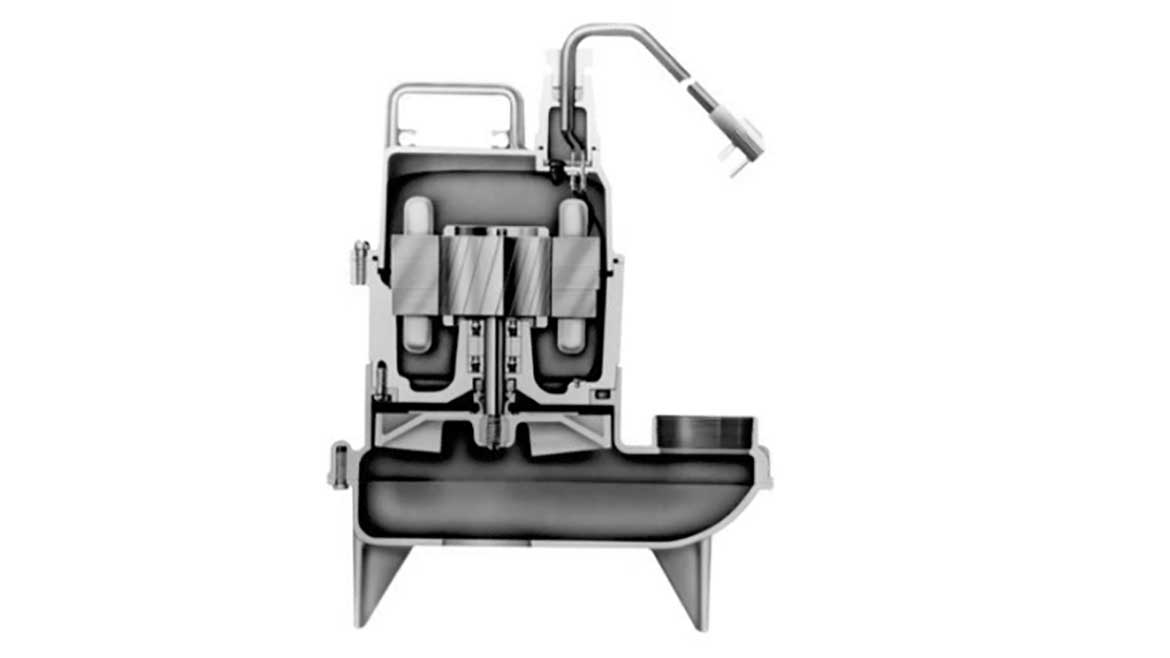
A vortex pump. Courtesy of Goulds Water Technology
Grinder pumps feature an actual cutting mechanism within the pump. The waste is first cut into smaller pieces before entering the inlet of the impeller. Grinders are typically used in high-head applications and with smaller pipes.
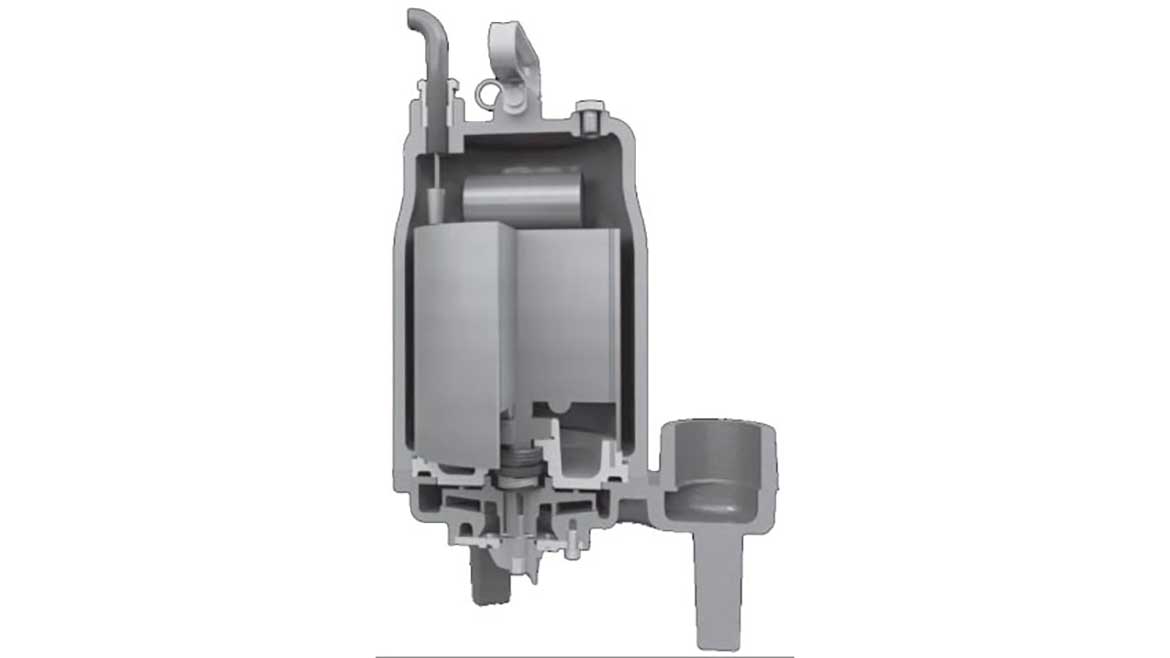
A grinder pump. Courtesy of Goulds Water Technology
Within each pump category, there are furthermore different price points available depending on the materials used, such as heavy-duty cast iron or more economical options with plastic components. When assessing pump sustainability, factors like specific use, manufacturing processes and material composition are critical. Cast iron pumps offer durability and a long lifespan, but their weight contributes to higher transportation energy consumption. On the other hand, plastic pumps can have a lower environmental impact during production but may be less durable over time.
As the wastewater industry is increasingly exploring more sustainable options, new materials such as corrosion-resistant carbon nanomaterials and recycled plastics are being developed, accompanied by increased adoption of automatic monitoring systems to minimize system downtime.
3. Required capacity
Required capacity is the flow or discharge capacity required by the installation. Selecting the right capacity will ensure proper functioning of a wastewater system. While flow can vary from installation to installation, asking, “How much waste do I need to get rid of?” is a good rule of thumb to handle most situations.
Residential and commercial applications differ in methods for calculating the capacity, split by volume.
For residential systems, two methods are commonly used. The first bathroom count method is based on the number of bathrooms, which corresponds to a flow rate per minute. The second method relies on fixture count (valve or tank) and refers to the "Hunter" estimate curves for demand load. By cross-referencing fixture count with the appropriate chart, the demand gallons per minute (gpm) can be determined.
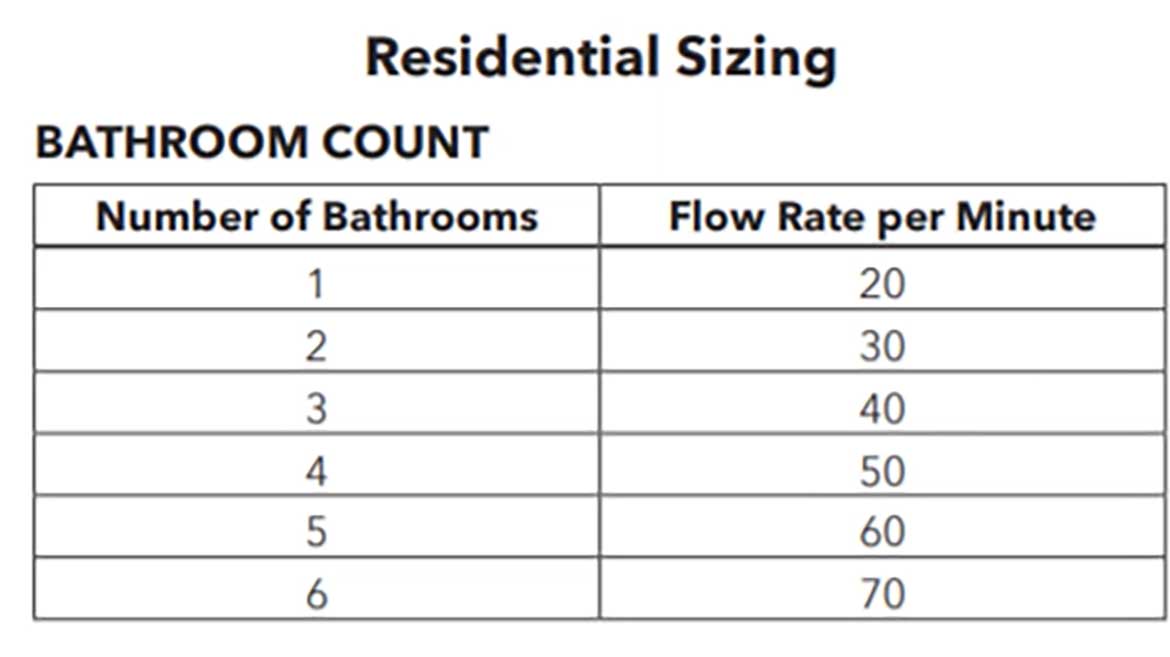
The ‘Bathroom Count’ method. Courtesy of Goulds Water Technology
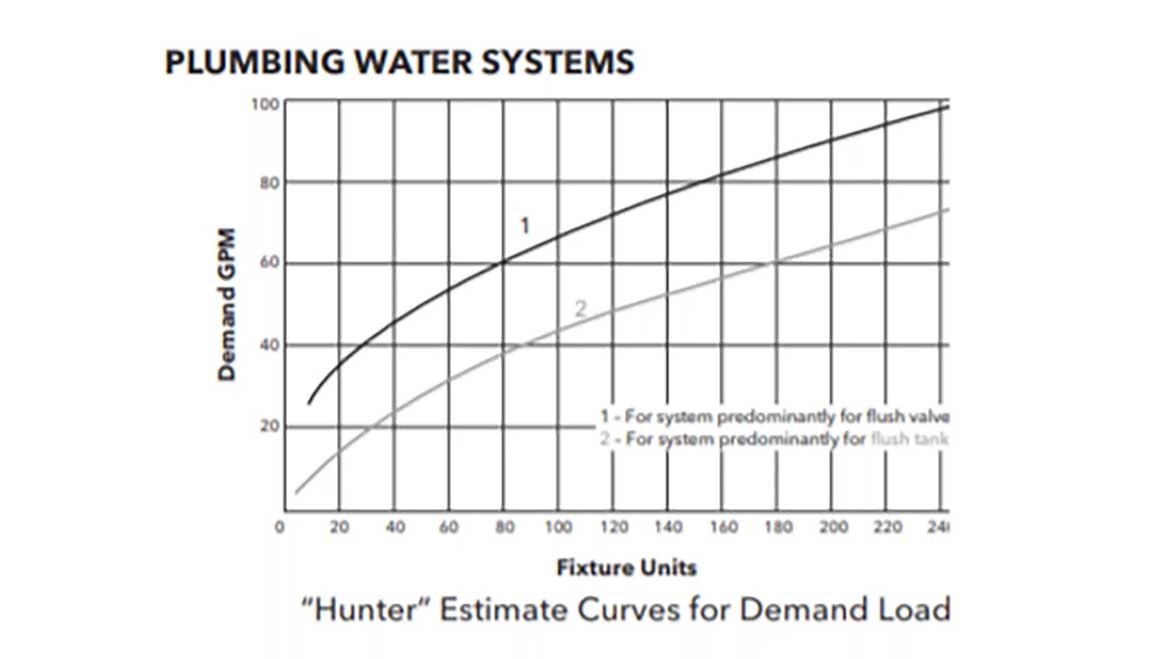
“Hunter” Estimate Curves for Demand Load method. Courtesy of Goulds Water Technology
In commercial systems, two methods are also employed, but on a larger scale — occupant sizing charts and the "Hunter" estimate curves for demand load. These methods provide a guideline for estimating the required GPM based on the number of occupants and other relevant factors. For more information, refer to Xylem’s Wastewater Technical Manual.
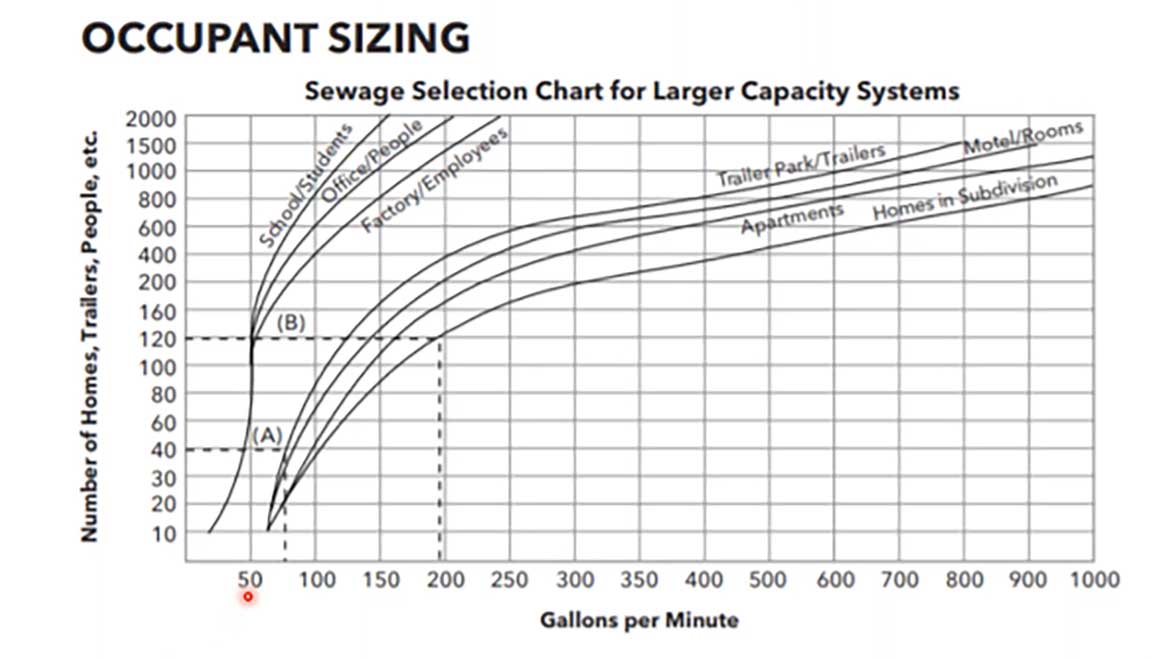
Commercial sizing. Courtesy of Goulds Water Technology
4. Sizing receiver basin and pipes for efficiency
Receiver basin: ensuring optimal performance
While electronic sizing programs excel in this step by performing complex calculations, there are some fundamental tips to consider when sizing the receiver basin for proper pump operation. The basin must be large enough to accommodate the pump, allowing enough room for wide-angle switch(es) to swing freely for proper operation. It should also provide adequate drawdown to guarantee a minimum run time (cycle time) for motor cooling, typically around one minute.
Additionally, the basin should have enough run time and flow volume to evacuate the liquid stored in the pipe at least one time per pump on cycle. An incorrectly sized receiver basin can disrupt the overall balance of the wastewater system, causing flow interruptions and increased friction loss, resulting in reduced pump efficiency, higher energy consumption and overall decreased system performance. As a starting estimate, use the pump capacity max flow and multiply it by 3 or 4 for the total basin size value.
Pipe size: ensuring proper flow
The discharge pipe should be capable of handling the size of solids in the system and have an outlet at least as big as the pump outlet. A general rule of thumb is to match the pipe size with the discharge size, ensuring efficient flow and preventing clogs.
The size of the piping can also affect the TDH calculation by influencing friction. Generally, larger pipes result in less friction and lower TDH. If the pipe size is too large, it can impact the velocity and increase costs. For example, a 2-inch pipe requires a minimum flow rate of 21 gallons per minute to properly scour the pipe during operation. It is crucial to maintain a minimum scouring velocity of 2 feet per second in the pipes to prevent clogging of pipe and fittings.
To calculate TDH, combine vertical lift, friction lift and pressure requirement in a certain wastewater system. Typical applications will not need to account for pressure.
Vertical lift + friction lift + pressure requirement = total dynamic head (TDH) in feet
5. Electric service: matching voltage, phase and amperage
The electric service for wastewater systems is like that of clean water systems. Submersible wastewater pumps are designed to run on either single-phase or three-phase service. Single-phase circuits provide voltage options of 115, 208, or 240 volts, while three-phase circuits offer 200, 230, 460, or 575 volts. The type of service available is typically determined by the power company.
Motors using three-phase service require overload protection. In the case of a panel, overload protection will be incorporated into the panel. Three-phase motors themselves do not have built-in overload protection. It is important to ensure that the voltage, phase and amperage of the pump motor and controls match the available service. Wastewater panels nowadays often offer multi-voltage options, requiring just one wire adjustment to match the available service.
Designing an efficient wastewater system requires careful consideration of factors such as state and local codes, solid handling size, required capacity, TDH calculations, receiver basin sizing, pipe size and electric service compatibility. By following these steps, an operator can select and size the appropriate wastewater pump, ensuring compliance, optimal performance and effective sewage handling. Investing time and effort in the design phase contributes to a system that operates efficiently and meets the specific needs of the application.